Cementovaný karbid je práškový metalurgický produkt spekaný vo vákuovej peci alebo pec redukcie vodíka s kobaltom, niklom a molybdénom ako hlavnou zložkou prášku volfrázového karbidu s vysokou náhodou s vysokým náhodným kovom. Singing je veľmi kritickým krokom v cementovom karbide. Takzvané spekanie je zahriatie práškového kompaktného na určitú teplotu, udržiavanie ho na určité časové obdobie a potom ho ochladiť, aby ste získali materiál s požadovanými vlastnosťami. Proces spekania cementovaného karbidu je veľmi komplikovaný a ak si nie ste opatrní, je ľahké vyrábať spekaný odpad. Chuangrui Xiaobian dnes s vami podelí o spoločnom spekanom odpade a dôvodoch.
1. Karbidový spekaný odpad je prvý, kto sa odlupuje
To znamená, že povrch cementovaného karbidu prechádza trhliny na okrajoch, deformácie škrupiny alebo trhliny a v ťažkých prípadoch malé tenké kože, ako sú šupiny rýb, prasknutia praskliny a dokonca aj putovanie. Odlupovanie je hlavne spôsobené kontaktným účinkom kobaltu v kompakte, takže plyn obsahujúci uhlík v ňom rozkladá voľný uhlík, čo vedie k zníženiu lokálnej sily kompaktu, čo vedie k odlupovaniu.
2. Druhým najbežnejším cementovým odpadom z karbidu sú diery
Póry nad 40 mikrónov sa nazývajú póry. Faktory, ktoré môžu spôsobiť pľuzgiere, môžu tvoriť póry. Okrem toho, keď sú v spekanom tele nečistoty, ktoré nie sú zvlhčené roztaveným kovom, ako sú veľké póry, ako napríklad „nesplnené“, alebo sintrované telo má vážnu pevnú fázu a segregácia kvapalnej fázy môže tvoriť póry.
3. Tretím najbežnejším cementovým odpadovým produktom spekaného karbidu je pľuzgier
Na povrchu zodpovedajúcich častí sa nachádzajú otvory v cementovom zliatine karbidu a na povrchu zodpovedajúcich častí sa objavujú konvexné zakrivené povrchy. Tento jav sa nazýva pľuzgiere. Hlavným dôvodom pľuzgierov je to, že spekané telo má relatívne koncentrovaný plyn. Zvyčajne existujú dva druhy: Jedným z nich je, že vzduch sa hromadí v spekanom tele a počas procesu zmršťovania sintrovania sa vzduch pohybuje zvnútra na povrch. Ak existujú nečistoty určitej veľkosti v spekanom tele, ako sú útržky zliatiny, zvyšky železa a kobaltové kúsky, vzduch sa tu sústreďuje. Keď sa spekané telo objaví v kvapalnej fáze a je hustotné, vzduch sa nedá vypustiť. Pľuzgiere sa tvoria na najmenších povrchoch.
Druhým je, že existuje chemická reakcia, ktorá vytvára veľké množstvo plynu v spekanom tele. Ak sú v spekanom tele nejaké oxidy, sú znížené po tom, ako sa zdá, že kvapalná fáza generuje plyn, čo spôsobí bublinu produktu; Zliatiny WC-CO sa všeobecne skladajú z spôsobených aglomeráciou oxidov v zmesi.
4. Existuje tiež nerovnomerná organizácia: miešanie
5, a potom je tu deformácia
Zmena nepravidelného tvaru spekaného tela sa nazýva deformácia. Hlavné dôvody deformácie sú nasledujúce: rozdelenie hustoty kompaktov nie je jednotné, pretože hustota hotovej zliatiny je rovnaká; Spekané telo lokálne chýba v uhlíku, pretože nedostatok uhlíka relatívne znižuje kvapalnú fázu; Nakladanie lode je neprimerané; Podporná doska je nerovnomerná.
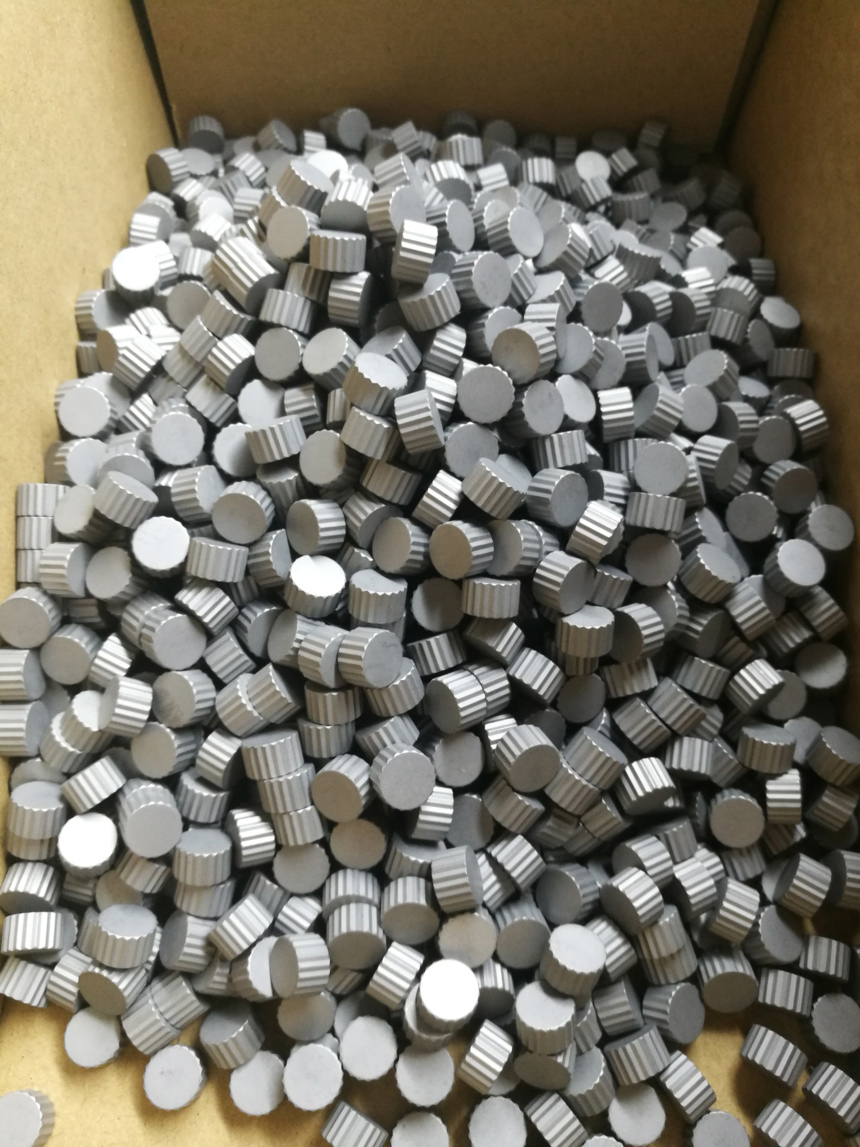
6. Čierne srdce
Voľná plocha na povrchu zlomenín zliatiny sa nazýva čierna stred. Hlavné dôvody: Príliš nízky obsah uhlíka a nevhodne vysoký obsah uhlíka. Všetky faktory, ktoré ovplyvňujú obsah uhlíka v spekanom tele, ovplyvnia tvorbu čiernych sŕdc.
7. Praskliny sú tiež bežným javom v cementovom karbidovom spekanom odpadových produktoch
Kompresné praskliny: Pretože relaxácia tlaku sa nezobrazuje okamžite, keď je briquette sušená, elastické zotavenie je počas spekania rýchlejšie. Oxidačné praskliny: Pretože briketa je čiastočne oxidovaná, keď je suchá, tepelná expanzia oxidovanej časti sa líši od expanzie neoxidovanej časti.
8. Prevodenie
Ak je teplota spekania príliš vysoká alebo je doba držania príliš dlhá, produkt bude prepustený. Nadmerné spaľovanie produktu spôsobuje, že zrná sú hrubšie, póry sa zvyšujú a vlastnosti zliatiny sa výrazne znižujú. Kovový lesk nedostatočne vystrašených výrobkov nie je zrejmý a je potrebné ho znova spustiť.
Čas príspevku: máj-31-2023